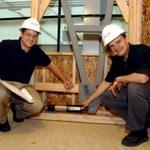
The dampers, which have never been tested before in wood construction, will be installed inside the walls of a full-scale, 1,800-square-foot townhouse - the world's largest wooden structure to undergo seismic testing on a shake table.
The unprecedented testing is part of a $1.24 million international project called NEESWood, funded by the National Science Foundation through its George E. Brown Jr. Network for Earthquake Engineering Simulation (NEES) program.
The goal of NEESWood is to safely increase the height of woodframe buildings in active seismic zones through the development of a design approach that considers a wide range of performance levels - from completely undamaged to almost collapsing.
The height of woodframe buildings traditionally has been limited to about four stories, mainly due to a lack of understanding of how taller structures might respond to earthquakes and other natural disasters. "We don't have accurate physical data to fully define how wood structures behave in earthquakes," said Michael Symans, associate professor of civil and environmental engineering at Rensselaer.
"We have some models, but their accuracy has not been verified with full-scale test data. This experiment will help us to further evaluate and refine those models."
Symans will be supervising the damping tests at the University at Buffalo's Structural Engineering and Earthquake Simulation Laboratory (SEESL), which is home to two adjacent three-dimensional shake tables where the test structure is anchored.
On July 6, a demonstration of the damper test will be open to the media, as well as broadcast live on the Web Here.
One approach to limiting the damage in woodframe structures is to look at the problem from an energy point of view, according to Symans. In an earthquake, the shaking ground imparts a certain amount of energy into the structure - energy that must eventually be dissipated.
During the earthquake, some of the energy is transformed to kinetic energy - moving a building from side to side - or to strain energy, in which the structural framing system becomes so deformed that it can be permanently damaged or even collapse. The goal of the dampers is to absorb a large portion of the earthquake energy, much like shock absorbers in a car absorb bumps in the road.
The damping system is essentially made up of fluid-filled shock absorbers installed horizontally throughout the walls of the house. "If we can channel some of the energy into the dampers, we can reduce the strain energy demand and thus reduce damage to the structure," Symans said.
The damping technology has been applied to steel and concrete buildings, but never before to wood structures. For the NEESWood experiment, the fluid dampers are being donated by Taylor Devices Inc., of North Tonawanda, N.Y.
"For the longest time, building codes have been prescriptive - the designer is told what to do to meet certain specifications, without explicit consideration given to the expected performance," Symans said. But lately there has been a shift in thinking as more large earthquakes have hit high-population areas.
About half of the approximately $40 billion in loss caused by the 1994 Northridge earthquake in the Los Angeles region was associated with wood structures, Symans notes, and this was much more damage than the general public expected. "The perception among building owners and the general public is that if a structure is built according to code, it will perform well during an earthquake," he said.
"This is true of snow, rain, and other typical severe weather conditions, but not necessarily for hurricanes and earthquakes."
Previous large-scale shake table tests have been performed on simple, box-like structures, but the NEESWood Project involves testing of a much more realistic building, Symans said. The townhouse in this experiment has balconies, an atrium, and other defining features that are more likely to be in the floor plan of a real woodframe residential building.
As the testing progresses, the team will be adding finish materials to the building, culminating in November with the violent shaking of the furnished, three-bedroom, two-bathroom townhouse - mimicking what an earthquake that occurs only once every 2,500 years would generate, according to Symans.
Phase 1 will be a benchmark test of the "bare bones" structure. Phase 2 will test the dampers on this benchmark building, and then finish materials will be added for each additional phase to test how these affect the response of the structure. Each phase will be run at increasingly higher levels of shaking, designed to simulate the increasing intensities that were recorded during the Northridge earthquake.